News Filter
Date
-
2011
-
2012
-
2013
-
2014
-
2015
-
2016
-
2017
-
2018
-
2019
-
2020
-
2022
News
Read the Winter 18/19 Newsletter
News Filter
Date
-
2011
-
2012
-
2013
-
2014
-
2015
-
2016
-
2017
-
2018
-
2019
-
2020
-
2022
News
ARENA Capital brings new investment to Earthmill Maintenance
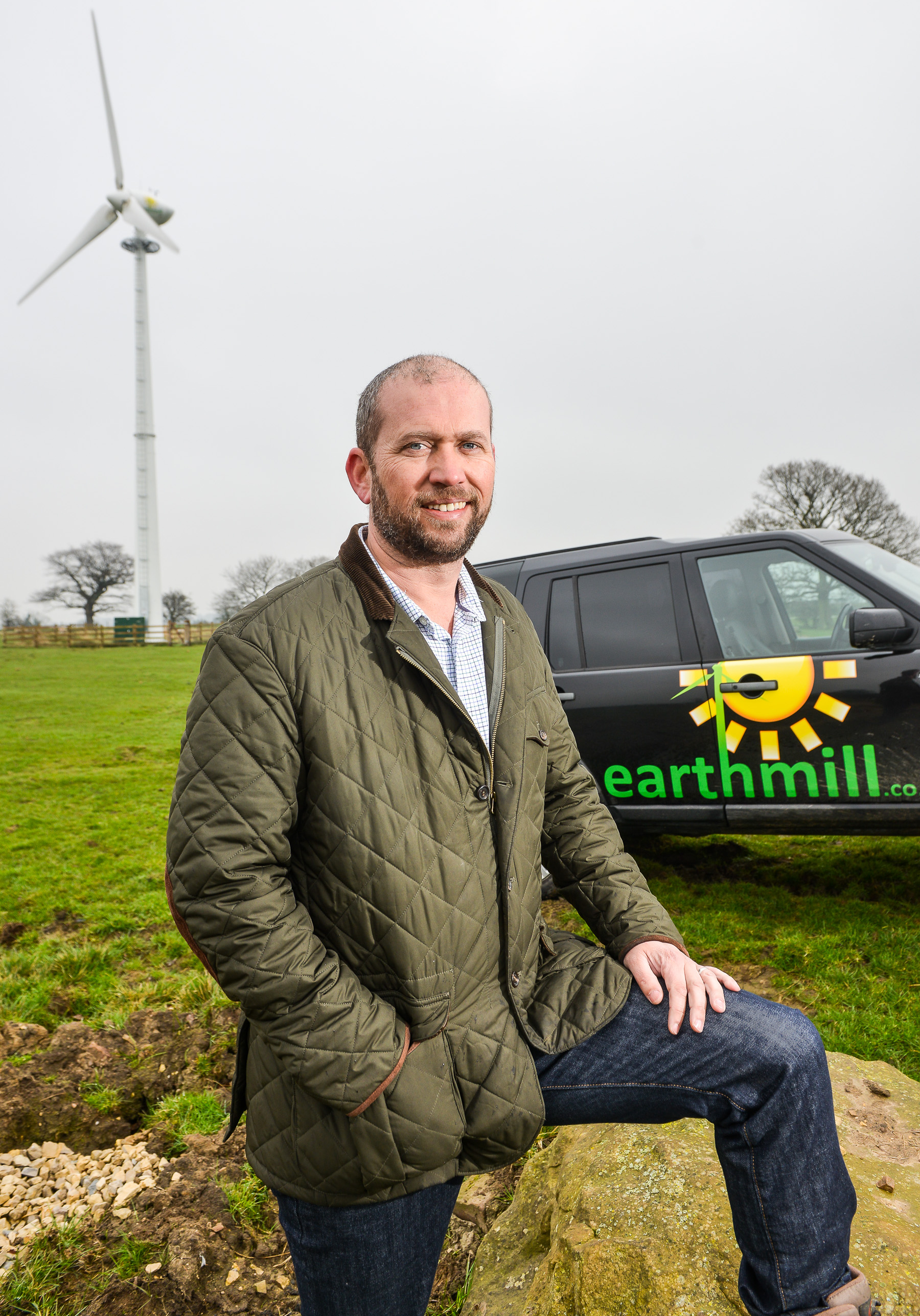
Turbine maintenance specialist Earthmill, which services more than 300 farm-scale turbines across the UK, has completed a deal with Arena Capital Partners that will see a seven-figure investment to grow the business over the coming years.
Arena Capital Partrners, which itself owns a fleet of 75 turbines, will become a majority shareholder in Earthmill following the investment. The firm is one of Europe’s leading specialist investors in wind energy ventures, with a portfolio of £40m invested in the sector.
Steve Milner, managing director of Earthmill, said: “It has been a challenging couple of years for the farm-scale wind industry with the Government prematurely ending the Feed-In Tariff, then manufacturers such as Endurance going out of business. We have had to completely restructure our business, and the work we do today goes way beyond standard maintenance.
“Since the launch of our maintenance business in 2016 we have worked really hard to grow our fleet and support our customers on farms across the UK who need spares, repairs and general servicing to keep their incomes ontrack.
“We had a fleet of less than 200 turbines under maintenance contract two years ago and we have grown that by 20%. We now have over £1m in spares stock, with engineers based around the UK, and we saw an opportunity to grow this business further and consolidate our position as the leader in farm-scale turbine after care,” he added.
The investment will see a boost in working capital, as well as a 25% immediate increase in clients from Arena’s 75-strong fleet of working turbines. Earthmill expects to grow stock levels to include larger items such as blades, gearboxes and generators to ensure quicker repairs. New engineers will join the team to broaden geographic coverage and reduce call out times for emergency repairs, decreasing down time and lost revenues when customers’ turbines lose power.
Commenting on the investment, Ian Greer CEO of Arena Capital Partners said: “The last few years have seen a great deal of consolidation as the wind energy market has stabilised. As the operator of a substantial fleet of turbines ourselves, we wanted to get smarter about how we maintained these investments.
“Earthmill has risen through the marketplace to stand out as an obvious partner for our fleet, but also as an investment opportunity that makes perfect sense,” he said.
“The new resources and increased capital, as well as the additional fleet will allow us to offer really good coverage in just about every UK location, and we look forward to bringing more customers on board as we increase our coverage across the UK,” added Mr Greer.
News Filter
Date
-
2011
-
2012
-
2013
-
2014
-
2015
-
2016
-
2017
-
2018
-
2019
-
2020
-
2022
News
Earthmill to support farm turbine owners following manufacturer collapse.
Steve Milner, managing director of Earthmill, said: “While the collapse of Endurance, in Canada and then here in the UK, has been a huge shock to everyone involved, by working together and taking swift collaborative action, the four service providers have been able to achieve the best possible outcome for turbine owners read more.
News Filter
Date
-
2011
-
2012
-
2013
-
2014
-
2015
-
2016
-
2017
-
2018
-
2019
-
2020
-
2022
News
Earthmill at YAMS 2017
A fantastic turnout at Yorkshire Agricultural Machinery Show 2017. The Earthmill stand was busy with new and existing clients discussing the Latest Endurance News and Service & Maintenance for Endurance E an X series turbines.
News Filter
Date
-
2011
-
2012
-
2013
-
2014
-
2015
-
2016
-
2017
-
2018
-
2019
-
2020
-
2022
News
Latest Endurance News
A copy of the correspondence to customers sent out by Earthmill’s Managing Director Steve Milner, providing an update regarding Endurance Wind Power.
Hi All,
I’m conscious that I haven’t sent an update out since December on Endurances insolvency and the various challenges this created.
Parts availability:
In my view this was the single most important issue, for example: The E series consist of 7600 separate parts 80 of which are bespoke, ongoing access is critical for the machines maintenance scheduled or otherwise. Earthmill have been working with the 3 other authorised service providers (Aeolus, Natural generation and Silverford), pooling our resources to set up a part supply operation which we completed early January. This will give us a central UK facility that can access and source all the known parts for the E series and X series turbines. Our aim is to have the top 100 items in stock and on hand for our combined fleet of 700 turbines
Endurance sale:
Grant Thornton were appointed as the Administrator for both the UK and Canadian business. They initially failed to find a buyer for the whole business as a going concern and have since broken the business up in to various parts to sell off.
A key part of the sale was the existing turbine parts inventory, within the UK operation there was over £600k of turbine parts which I’m very pleased to confirm we have successfully bid for. We are currently in the process of checking the inventory at the factory and transferring across to the new parts operation. This gives us a great starting inventory for the parts operation.
Service and maintenance charges:
Our standard service and maintenance contract covers the costs of all scheduled servicing (excluding consumables and parts), however if you do require engineers on site outside of normal servicing, visits are chargeable. Fees are based on two climbing engineers on site, Initial call out charge and first hour on site: £180, thereafter hourly rate of £110 Ex Vat. Our typical call out ratio is 1 site visit per turbine per year. That said 9 out of 10 issues can be resolved remotely via the office team, if however we do need to attend site we will always aim to discuss any charges with you in advance.
Insurance:
Certain insurers have been requesting that clients have an O&M contract in place with ourselves or one of the other ASP’s mentioned above before they will renew a policy, we have been in touch with all clients who needed a new contract if we haven’t spoken to you then please don’t be concerned as this just means you’re existing service agreement is sufficient.
Earthmill:
The new government was fairly quick to cut back on renewable support, which effectively stopped the on shore wind industry in its tracks. As result we have spent the last 18 months restructuring the business around the service and maintenance of existing clients. We currently maintain over 250 Endurance turbines and have expanded our service team/office support to ensure that we are able to offer the support levels required.
If you do require any further information on your existing service contract or any other related issues please feel free to call the operations team on 01937 581011 or send us and email.
Regards
Steve Milner
News Filter
Date
-
2011
-
2012
-
2013
-
2014
-
2015
-
2016
-
2017
-
2018
-
2019
-
2020
-
2022
News
Latest news regarding Endurance Wind Power
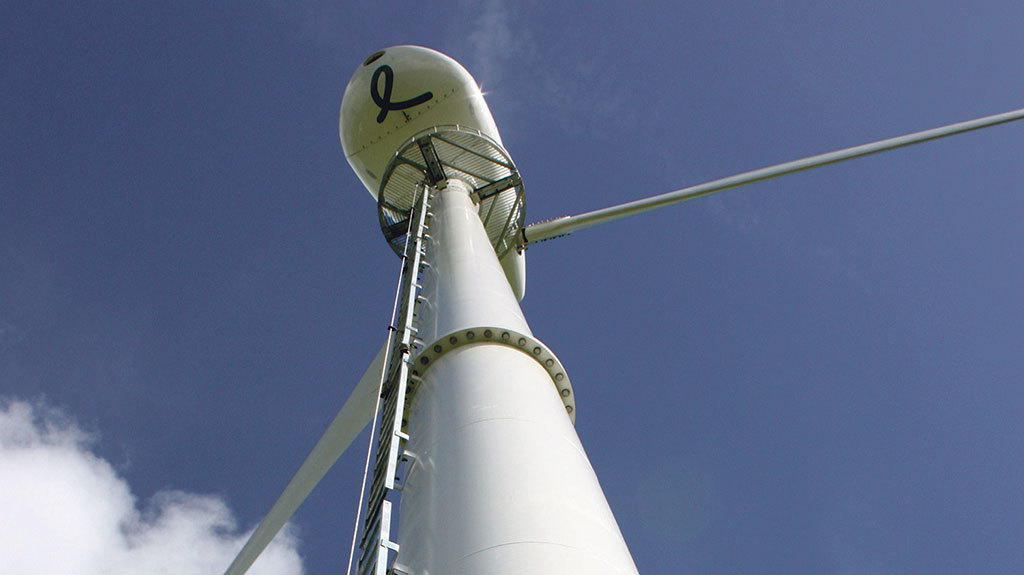
Farmers Guardian Insight: Wind Turbine owners offered support after collapse of manufacturer Endurance. The five Endurance Authorised Service Providers (ASPs), which are all independently owned businesses based in the UK, have agreed to provide continuing support to all the firm’s UK customers, and to ensure stocks of spares and parts will remain readily available read more.
Vancouver Sun: A bankruptcy notice on the front door of Endurance Wind Power in the Campbell Heights industrial area on 24th Ave. near 192 St. confirms that the company’s operations are now being overseen by trustee Grant Thornton Ltd read more.
Farmers Weekly: Farmers and landowners with turbines built by Endurance have been assured they will get continued technical support after the Canadian manufacturer was declared bankrupt last week. It is understood that manufacturer warranties on turbines bought through the Canadian parent firm (namely E-Series turbines) and no longer valid, while the future for X-Series warranties depends on the fate of the UK arm of Endurance read more.
News Filter
Date
-
2011
-
2012
-
2013
-
2014
-
2015
-
2016
-
2017
-
2018
-
2019
-
2020
-
2022
News
Endurance Update
A copy of the correspondence to customers sent out today by Earthmill’s Managing Director Steve Milner, providing an update regarding Endurance Wind Power.
Dear Sir / Madam,
I’m writing to inform you that unfortunately Endurance’s Canadian operation was closed last week and have ceased trading. I understand that an administrator has been appointed and we anticipate an announcement regarding the future of their UK subsidiary within the coming days.
This situation is still not fully understood as we have had no UK announcement, however I didn’t want to leave it any longer to communicate the situation to our clients. The main impact should Endurance UK follow Canada is parts availability (for the bespoke parts) and the loss of a manufacturer warranty.
I appreciate this is a concerning situation for you as turbine owners, but please rest assured we are working hard to make sure we have as much in place as possible to limit any impact of this change. We are currently working with the 4 other approved maintenance companies with a plan to pool our resources to source and hold key parts, equipment and host monitoring software to ensure we can continue to fully support our and your turbines.
Our immediate objective is to establish what is happening to the UK operation and limit the impact this will have on supply chain and client support. Therefore I would hope to update you on the situation as the week progresses; as soon as we get more news will update you. If you wish to call to discuss in more detail with myself or the team please call the office on 01937581011.
Regards,
Steve Milner
News Filter
Date
-
2011
-
2012
-
2013
-
2014
-
2015
-
2016
-
2017
-
2018
-
2019
-
2020
-
2022
News
Earthmill announced as Endurance Authorised Service Provider
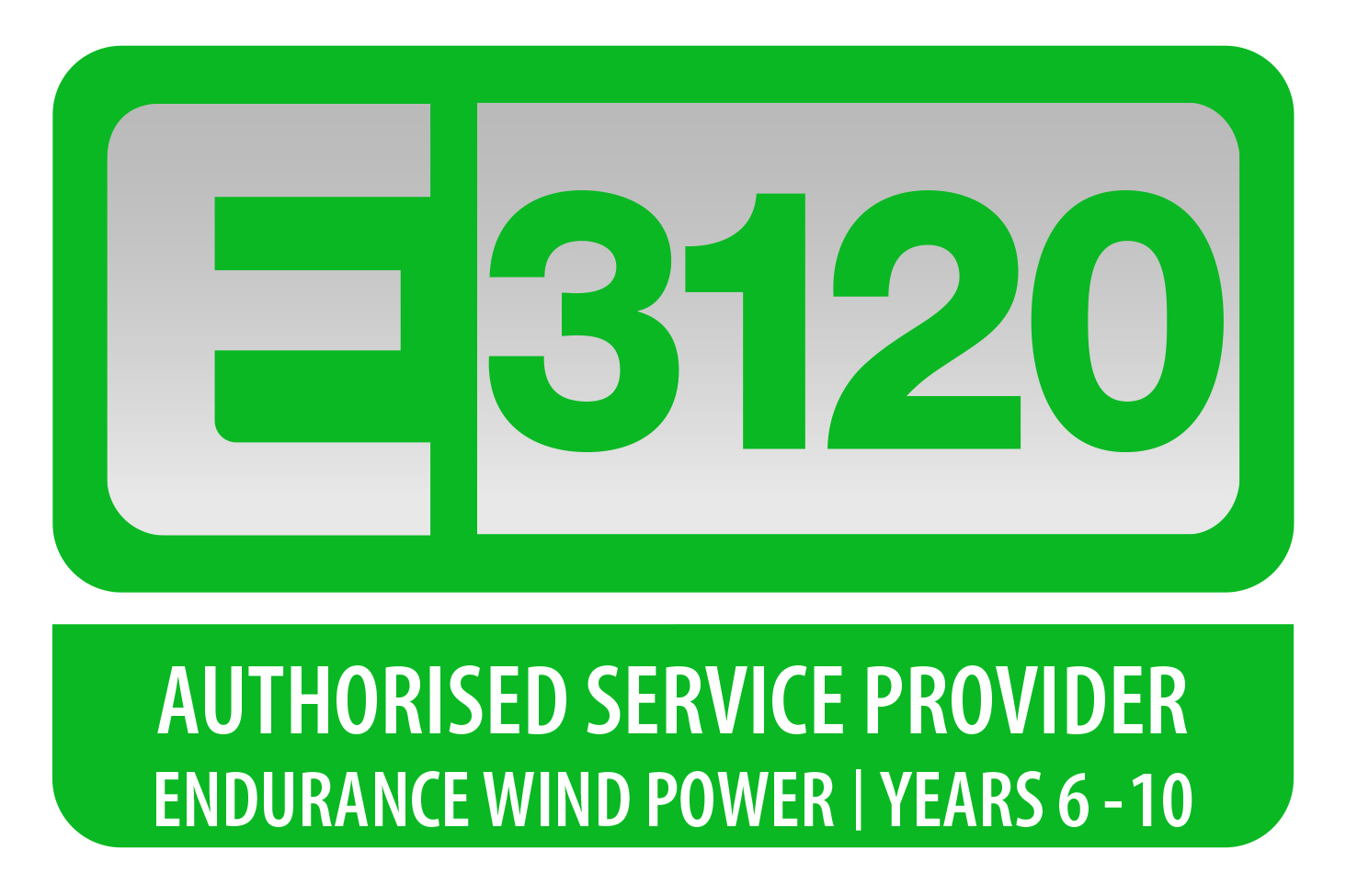
Earthmill are proud to announce that they have been selected by Endurance Wind Power as an Authorised Service Provider (ASP) for the E-3120 wind turbine for the North of England and Wales.
Whether you are coming to the end of your warranty period or simply looking for a better service which won’t affect your manufacturer warranty, Earthmill have a service and maintenance package to suit you.
By choosing a selected ASP to manage your turbine you will unlock a number of benefits that are otherwise unavailable allowing for greater availability levels and ultimately a better return on investment.
- Increased Parts Availability – With over £25,000 worth of spare parts and consumables kept in stock and fast track priority access to Endurance’s UK warehouse – You’ll spend less time waiting for parts and more time generating power.
- Specially Trained Technicians – Our ASP technicians & engineers are trained to the highest level by Endurance to perform work such as laser alignment and blade swaps which can usually only be performed by the manufacturers.
- 24 hour remote monitoring & technical support – Your turbine’s health and performance will be monitored around the clock, 24 hours a day with Earthmill monitoring live from our head office control centre during office hours and Endurance taking over outside of these times. In the majority of cases we are able to restart your machine remotely resulting in less down time.
- Fast Response – In the event that a site visit is required, all our engineers carry vehicle trackers which allow us to deploy them efficiently as possible,
- Pre warranty Inspection – Prior to the end of your warranty period, Earthmill technicians will carry out a comprehensive inspection & health report on your turbine checking its key components and assessment of the generation performance compared against the manufacturer’s power curve. Any issues found will be registered with the manufacturer for rectification under the original warranty program and remedied as soon as possible.
- Scheduled Maintenance – Earthmill engineers will provide scheduled servicing and report in line with the manufacturer’s current guidelines at the prescribed service intervals, typically every 5000 rotational hours.
- Unscheduled Maintenance – The service agreement provides for up to 2 unscheduled visits to site each year or 16 hours on site (whichever the greater).
- Free Software Updates – Endurance will provide free software for you to monitor the performance of your turbine from anywhere in the world as well as free turbine software updates as released which can improve performance and efficiency.
- Better Export Rates – Export rates constantly change and we work with a number of suppliers pooling our turbines to secure the best rate available, whilst this may be fractions of a penny it all adds up. On average a 1p increase in export is worth £1500 per annum for a low energy user.
- Business Rate Management & Insurance Advice – Business rates demands vary depending on location. We have successfully advised and negotiated down a number of business rate demands clients have received. With ASP Earthmill will ensure you are getting the best rates possible. Getting the best insurance rates and more importantly the correct level of cover is also another added saving and area we regularly advise on.
Whilst all of the above sounds impressive, the proof is in our track record. Whilst the industry average for turbine availability is 95%, Earthmill maintain a 98% average. This additional availability is worth on average £1,200 to each of our customers every year.
To find out more about how you can benefit by changing your wind turbine service provider to an ASP, please call 01937 581011 or fill out our online contact form and we will contact you.
News Filter
Date
-
2011
-
2012
-
2013
-
2014
-
2015
-
2016
-
2017
-
2018
-
2019
-
2020
-
2022
News
How does a biomass CHP plant work?
The Arbor ElectroGen 45 biomass CHP plant generates both heat and electricity by gasifying sustainably sourced woodchips at high temperatures. Woodchips (or ‘woody biomass’) are fed into the plant automatically from the hopper, at which point the gasification process begins:
The Arbor ElectroGen gasifies fuel at a high enough temperature that virtually zero tar, nitrates or particulates are produced during the process, resulting in exceptionally low emissions.
A high energy and heat user can expect a yearly net benefit from a single CHP plant of approximately £97,000.